Strata Manufacturing (Strata), the advanced manufacturing company wholly-owned by Mubadala Investment Company PJSC, is celebrating 12 years of extensive collaborations with Airbus.
The decade-plus collaboration has resulted in the Al Ain-based manufacturer’s lightweight composite components, which carry its ‘Made with Pride in the UAE’ trademark, on wide body fleets around the world. The cross-border collaboration with the European aircraft maker has also seen Strata establish dedicated manufacturing lines for some of the world’s most advanced aircraft – including the A350, the first long-range, wide-body Airbus jet largely made of carbon fibre reinforced composite – in the heart of Al Nibras Aerospace Park.
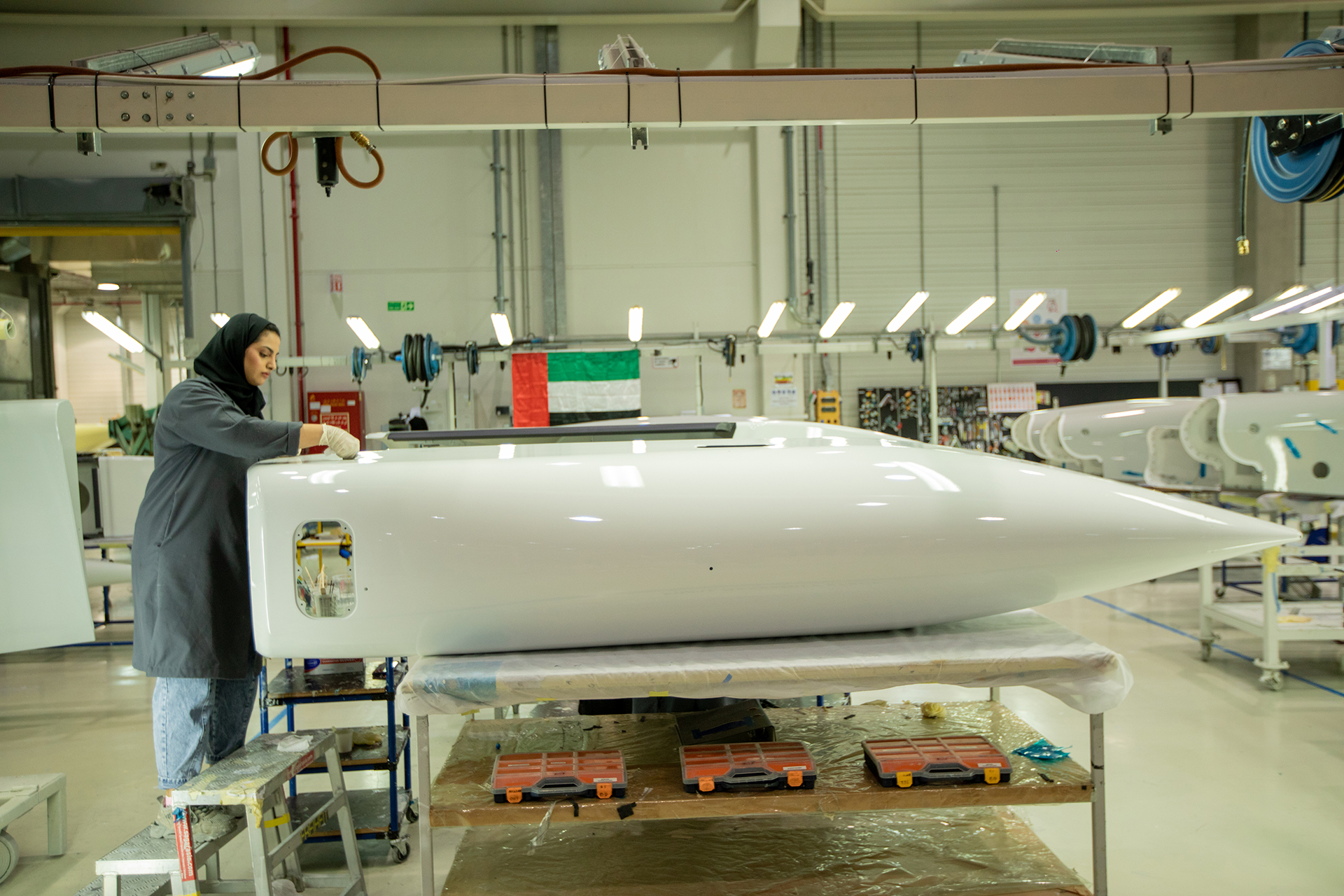
Since entering production, Strata has become a leader in composite aerospace structures for international airplane manufacturers – Airbus and Boeing included – to build more fuel-efficient planes and limit carbon emissions.
The total composite delivered to Airbus since contract signed is 1,387 shipset including A350 – 800/900/1000s (400), A330 Flap Track Faring (FTF)/Spoilers/Aileron Assembly (800), and A380 (187). Today, the UAE manufacturer is the sole source supplier of Aileron Assemblies for the A330 programme, delivering two shipsets a month. The agreement between Airbus and Strata was extended in September 2021 for Aileron until the end of the programme.
“While recent years have seen aviation attract a negative reputation when it comes to sustainability, the industry has proven throughout its history to be one of the most technologically advanced and innovative sectors focused on delivering faster, cheaper, and less environmentally harmful travel,” said Strata’s CEO Ismail Ali Abdulla. “The industry has a progressive record of fuel efficiency, with next-gen aircraft like the A350 consuming, on average, less than three litres per 100 passenger kilometres. Fuel burn per passenger-kilometre has halved since 1990, according to the International Air Transport Association.”
In addition to the sustainability focus on fuel efficiency in aviation, Ismail Ali Abdulla insists composite manufacturing and 4IR technology in the production process can play a significant role in aiding the industry’s path to zero emissions.
“The use of carbon composite materials to build aircraft components deliver exceptional gains in environmental performance by improving fuel burn through airframe efficiency,” added Ismail Ali Abdulla.
In August 2020, Strata successfully delivered the 100th shipset of Inboard Flaps (IBF) for the Airbus A350-900 programme. More than half (53 per cent) of each Inboard Flap was built using light composite materials to reduce fuel consumption and operating costs, improve passenger comfort and lower environmental impact. Strata produced the Flaps using a fully automated manufacturing process comprising Hot Drape Forming (HDF) and computer-controlled robotic Automated Tape Layup (ATL) machines.
“We successfully moved from assembling imported parts to fabricating IBF components internally, totally justifying our investment in developing new technologies,” explained Ismail Ali Abdulla.
Strata’s HDF machine pre-forms carbon fibre components for aircraft parts and enables faster production of high-quality composite parts, while an infrared radiation heating system quickly and evenly softens carbon fibre, delivering accurate parts free from wrinkling.
Strata’s two (ATL) machines lay unidirectional prepreg materials onto a flatbed before being transferred to a mould for further processing. The machines’ work envelope of 2.5 meters by 10 meters enables automated processing of large composite layups, eliminating the need for a separate ultrasonic cutting machine, and drastically reducing processing times.
“The entire industry, whether in the UAE or elsewhere, will see a shift towards artificial intelligence (AI), digitalisation, automation, 3D printing, robotics, and overall advanced technology adoption to address the cost challenges resulting from the COVID-19 induced air transport downturn. We have all predicted these innovations will impact the manufacturing sector, but investment in smart manufacturing and automation has been slow – only now is it being accelerated. This is where Strata overperforms as early adopters of advanced and transformative 4th Industrial Revolution technology. Our R&D function, for instance, is focused on developing advanced manufacturing technologies to support current and future programmes in collaboration with local universities, technology partners, and OEM customers,” explained Ismail Ali Abdulla.
Strata’s R&D programme encompasses two state-of-the-art research labs – one at Strata’s facilities, the other at Abu Dhabi’s Khalifa University, where 13 live projects cover additive manufacturing, advanced inspection techniques, optimised processing and machining of composite parts, robotic assembly, artificial intelligence, and data analytics.
“Going forward, we predict the industry will see a huge (AI) uptake to deliver crucial data and analytics that provide deep insights and allow manufacturing operations to swiftly adapt to demand changes. These disruptive technologies will create a more resilient supply chain,” added Ismail Ali Abdulla.
Prioritisation of its technology strategy and workforce upskilling will, insisted the CEO, leave Strata well placed to meet the post-pandemic demand upturn where fleet replacement will take centre stage in an industry focused on utilising more fuel-efficient aircraft.
“At Strata we take a very pragmatic view of the disruption caused by COVID; we prefer to see it as an opportunity to reassess, focus on industrial improvements, and reshape our manufacturing offering for the future. Through advanced technology adoption, we look to become more effective and efficient, speed up delivery schedules and surpass quality and sustainability goals,” concluded Ismail Ali Abdulla.