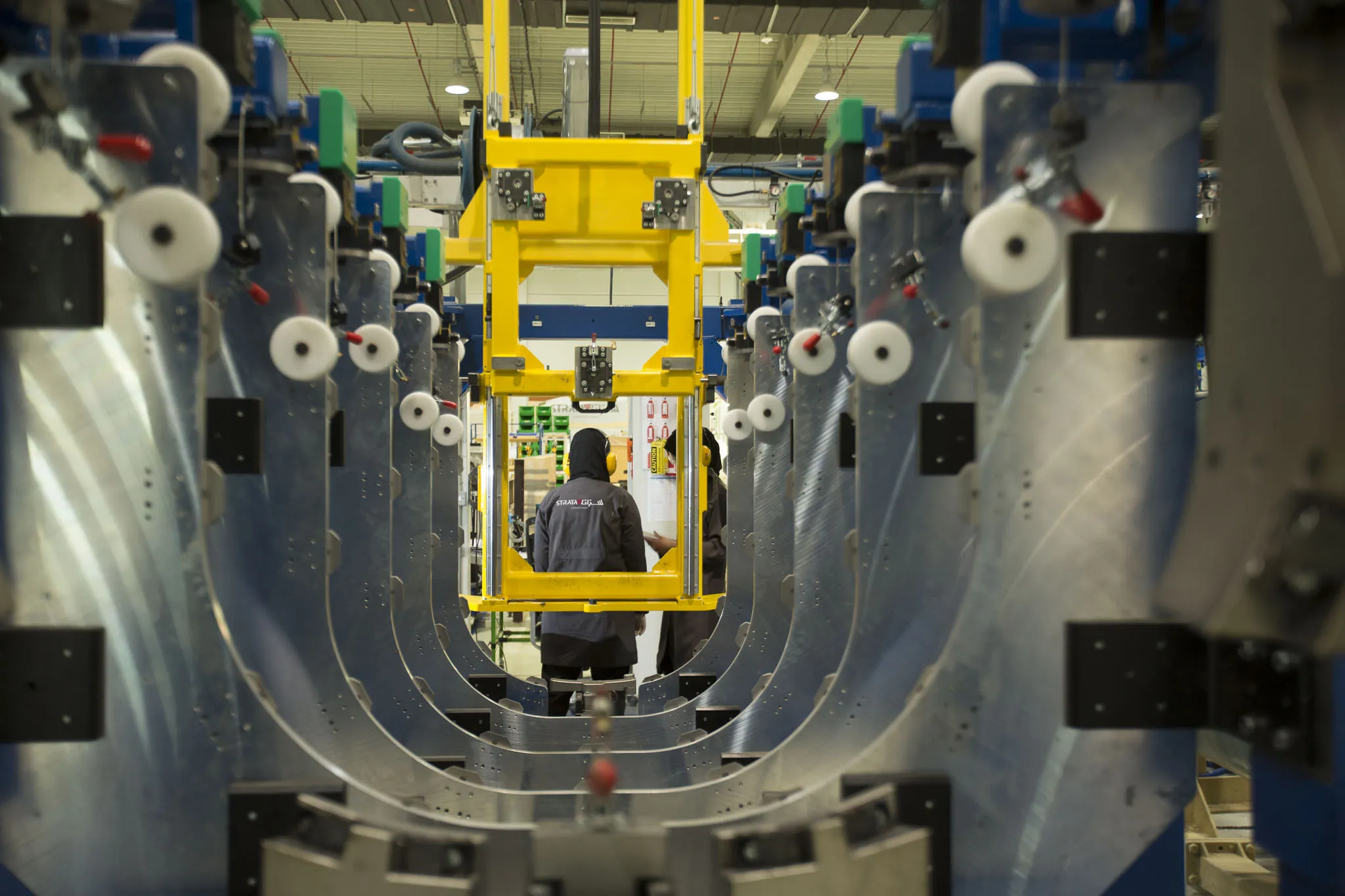
Our Facility
Serving You With Pride
Our state-of-the-art facility was built in Al Ain in 2009 and boasts 37,000 sqm of production floor space.
Focused on build-to-print production of primary and secondary aerostructures utilising advanced composite materials, our Al Ain center is a superlative example of our dedication to excellence.
The facility was qualified in 2010 and is certified as follows: NADCAP, EN9100, and qualified by the Original Equipment Manufacturer (OEMs).
Further qualifications at Al Ain include NADCAP Composites, NADCAP-NDT, NADCAP Chemical Processing, EN9100:2016, ISO 14001:2015, and OHSAS 1800:2007.
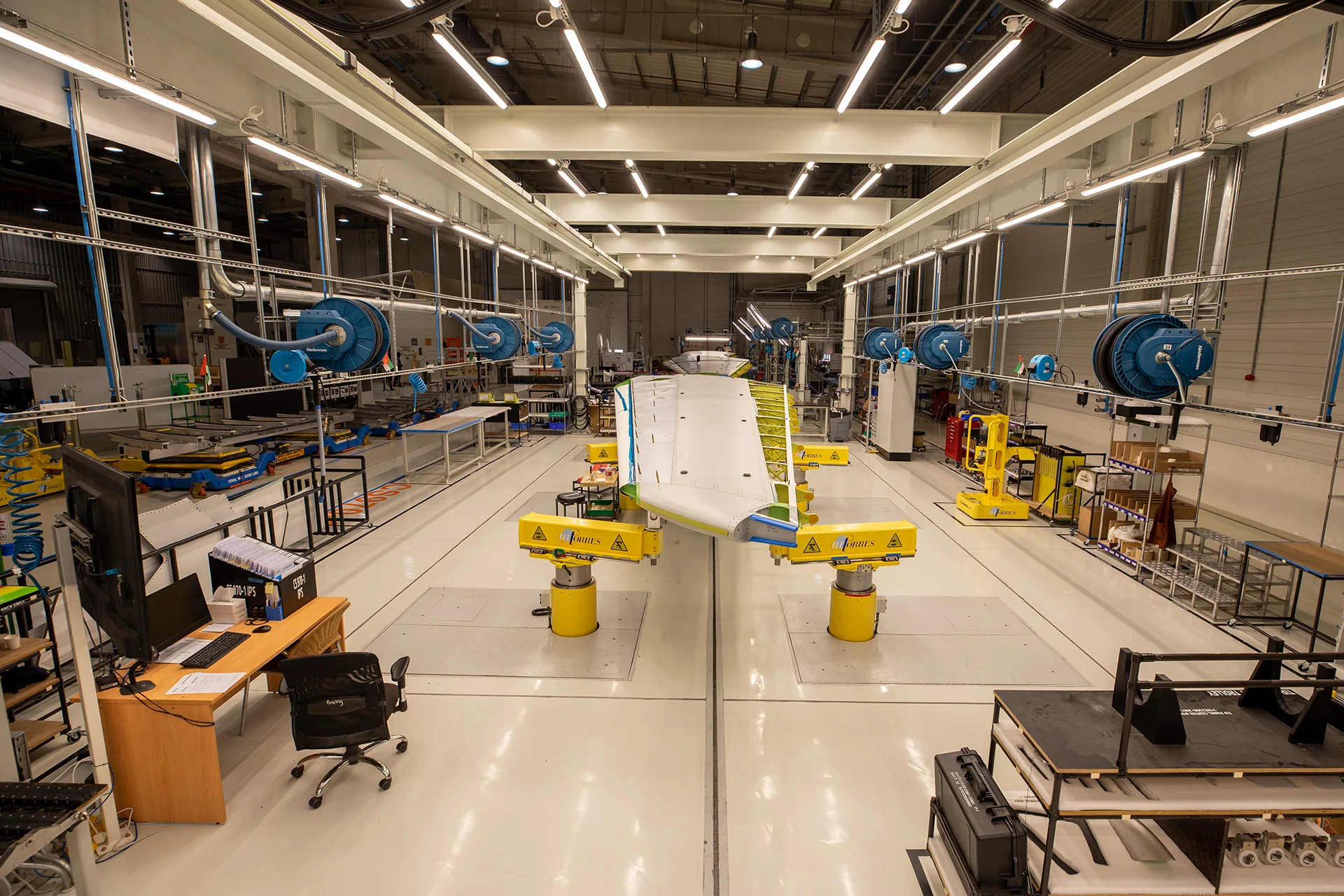
Strata is strongly positioned to diversify into new advanced manufacturing verticals. We aim to achieve this by leveraging our existing capabilities, and through these verticals, we aspire to:
- Develop an array of profitable, sustainable, and disruptive projects
- Gain a clear competitive advantage by building on existing STRATA & Abu Dhabi capabilities
- Further enable the UAE private sector, creating opportunities for local SMEs
- Support the growth of national industries and enhance their global competitive edge, in line with UAE’s industrial strategy (Operation 300bn)
- Contribute to UAE clusters strategy, by developing national champions and scaling promising ventures
- Contribute to Abu Dhabi’s socio-economic objectives and lay further foundations for future growth
Laboratory
- Strata relies on excellence throughout every stage of the production process. At the center of this lies our laboratory, which provides mechanical and physical testing for all of the critical materials we utilise.
- Our laboratory is fully qualified by Strata’s key clientele as well as by international regulatory authorities. This process of ensuring the utmost in quality and consistency guarantees that materials - such as glass or carbon fiber - are suitable for us and our customers
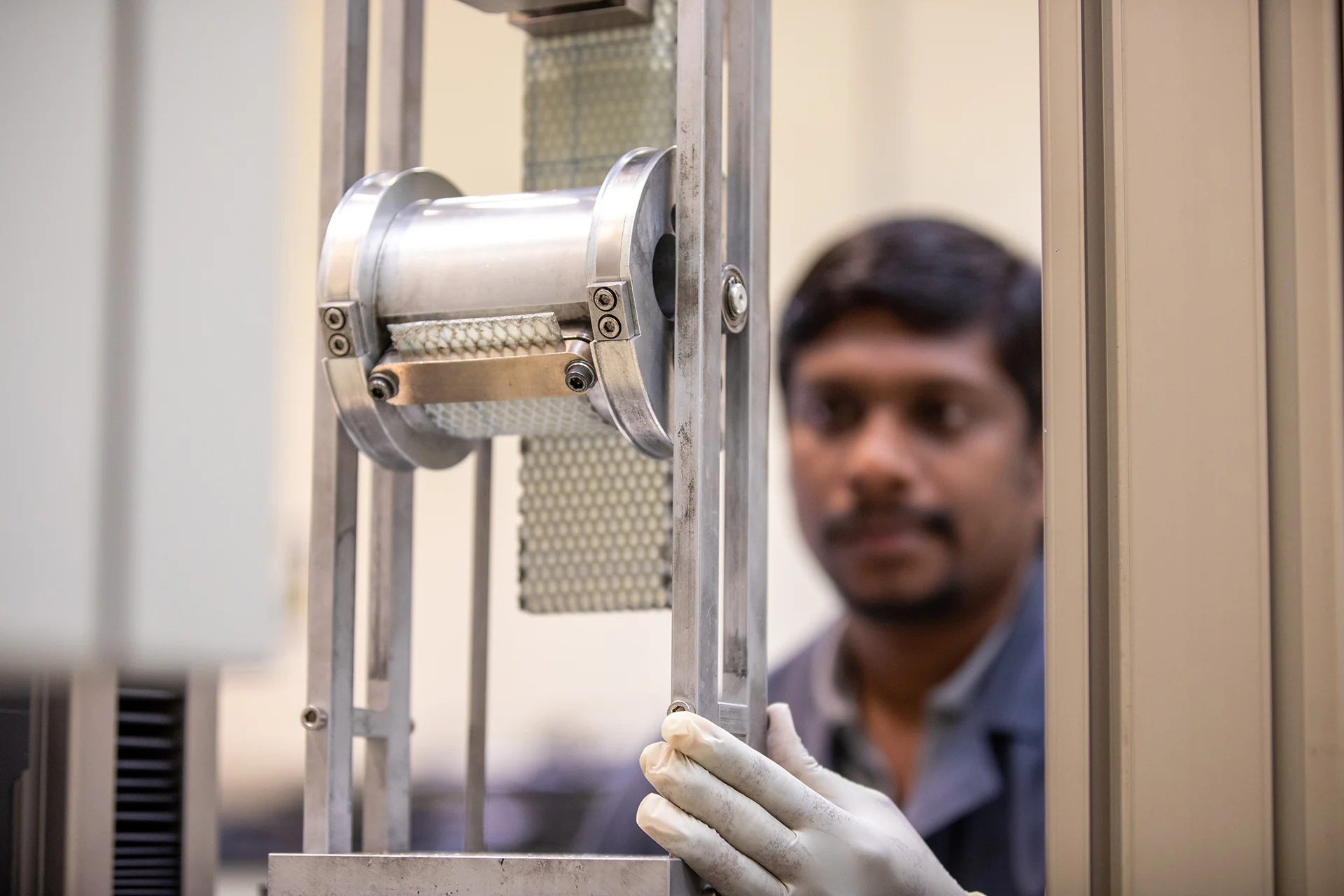
Composite Honeycomb Machining
- At our Composite Honeycomb Machining Area, we manufacture the honeycomb cores used across a variety of productions. These cores increase the stiffness of laminates, by thickening them with a low-density material.
- The result is a dramatic increase in sturdiness, coupled with very little additional weight - a primary objective for effective manufacturing for the aerospace industry.
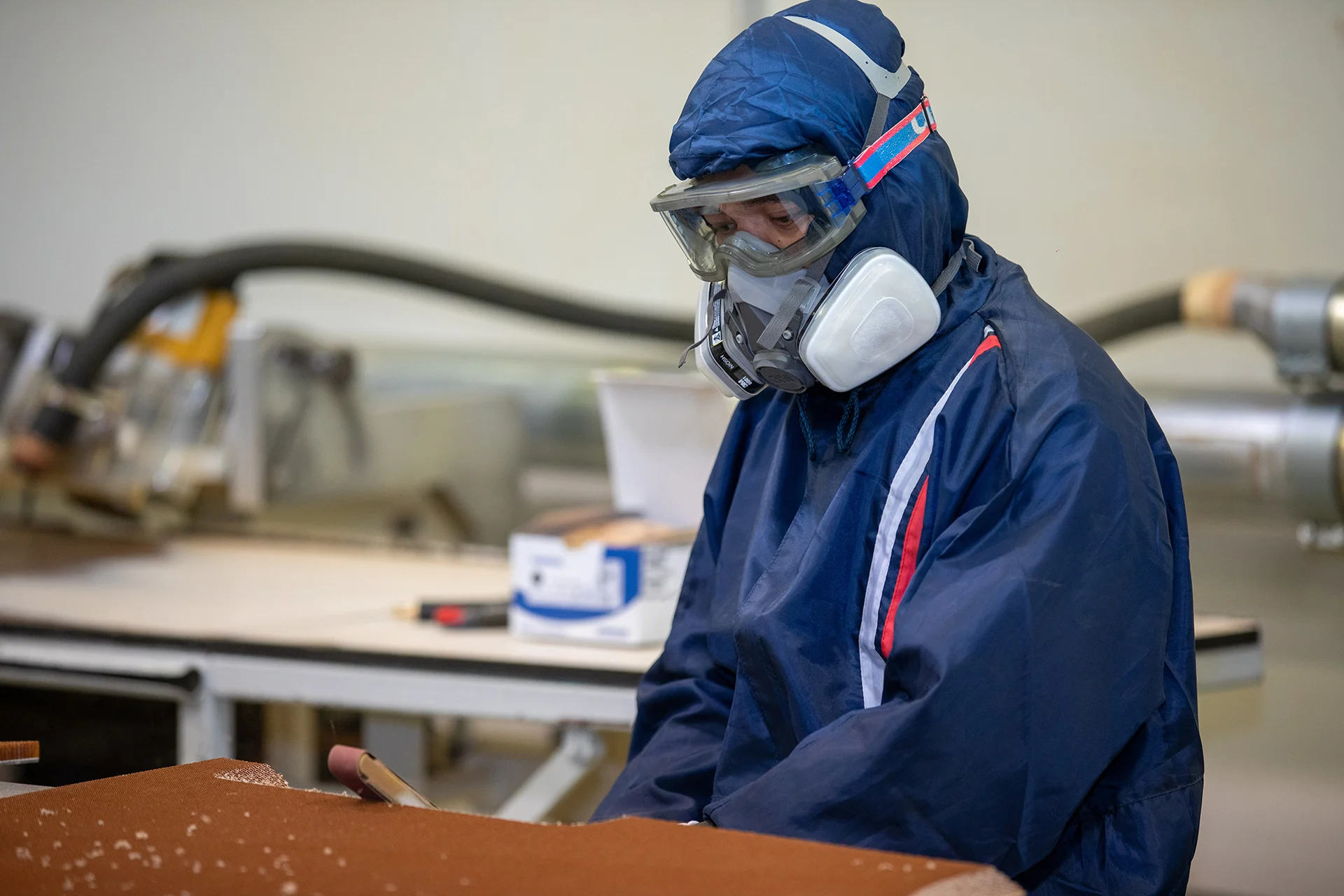
Contamination Controlled Area (CCA)
- Strata has invested in a cutting-edge Contamination Controlled Area, also known as a ‘Clean Room’. Our CCA covers 4000 sqm, and has been meticulously designed according to ISO Class 8 specifications. This means the air is filtered 10 times per hour, positive pressure, and temperature, relative humidity and dust particle counts are all tightly controlled and subject to 24/7 monitoring.
- It is here our prepreg materials (glass and carbon fibre) are cut to size with our three ply-cutting machines, which bring engineering drawings to realisation with an industry-beating accuracy of +/- 1mm. The resulting plys are then delivered to our lay-up stations, where our skilled Aerostructure Technicians use a laser projection system to ascertain the precise location for the ply to be laid within a mould tool. Vacuum pressure is applied to eradicate all air between the layers, and then applied again in preparation for the autoclave cure cycle. In accordance with our quality standards, the vacuum bags are checked for leaks every time they’re removed from the clean room, and must not show a loss of pressure over 0.2 bars across 5 mins.
- It’s due to such attention to detail, and because such meticulous systems are put in place that Strata maintains its position as an industry leader.
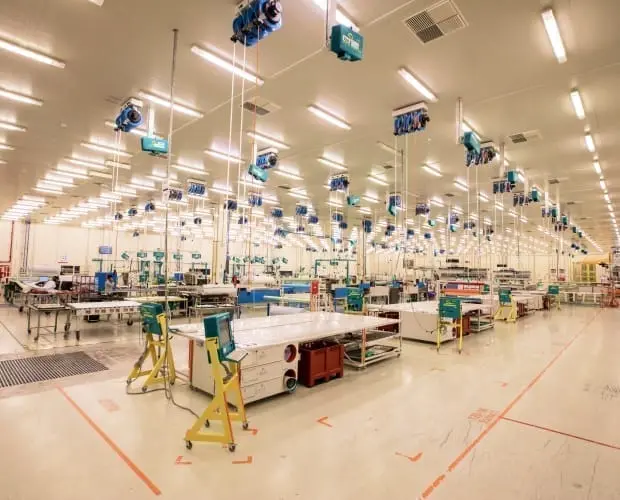
Autoclave
- Using a highly precise combination of heat, pressure, and vacuum, autoclaves transform our prepreg materials into strong, durable, and sturdy parts.
- We utilise nitrogen in our autoclave, due to the fact this inert gas will not cause combustion at any point of the autoclave cure process. During this process, a pressure of up to 10 bars is applied under temperatures that reach up to 250C for approximately six hours.
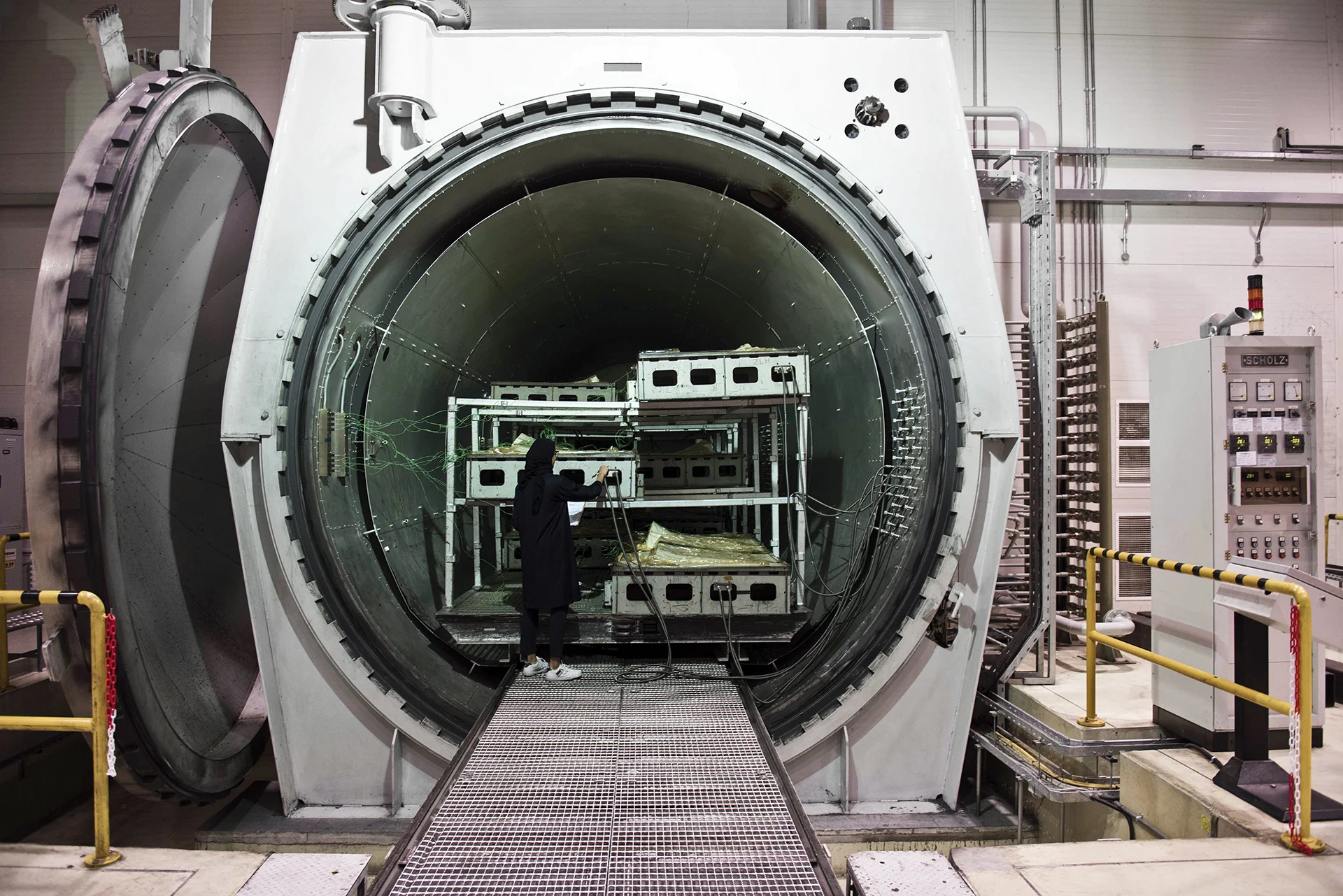
Computer Numerical Control (CNC)
- Our four 5-Axis CNC Machines (Computer Numerical Control) are responsible for trimming the products to the precise specifications requested by our clients. In aerospace manufacture, even a fraction of a centimeter can make all the difference, meaning precision and accuracy is always at the forefront of our minds and the tools we use.
- These machines can cut up to 65 meters per minute and are accurate to within 0.02mm - the average thickness of a single strand of human hair.
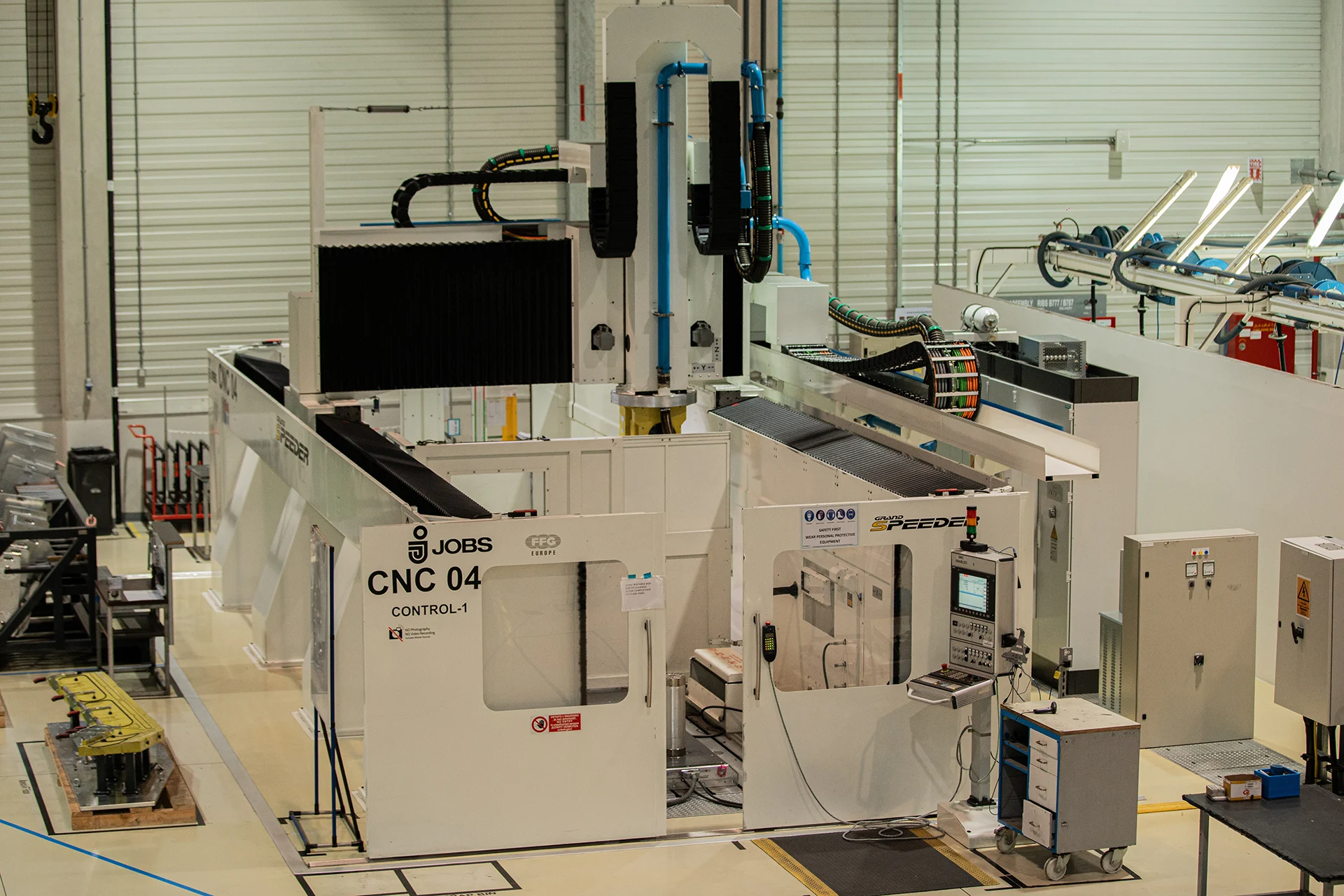
Non-Destructive Testing (NDT)
- At Strata, we use Non-Destructive Testing (NDT) to ascertain and confirm the quality and conformity of all the bonded products produced in the CCA.
- We use a variety of innovative approaches, which include A-Scan, 3-axis C-Scan, 10-axis C-Scan, X-Ray, phased array, and manual tap testing. With these processes, Strata can accurately determine each product’s quality, and in doing so, meet the exacting standards set by our valued clients.
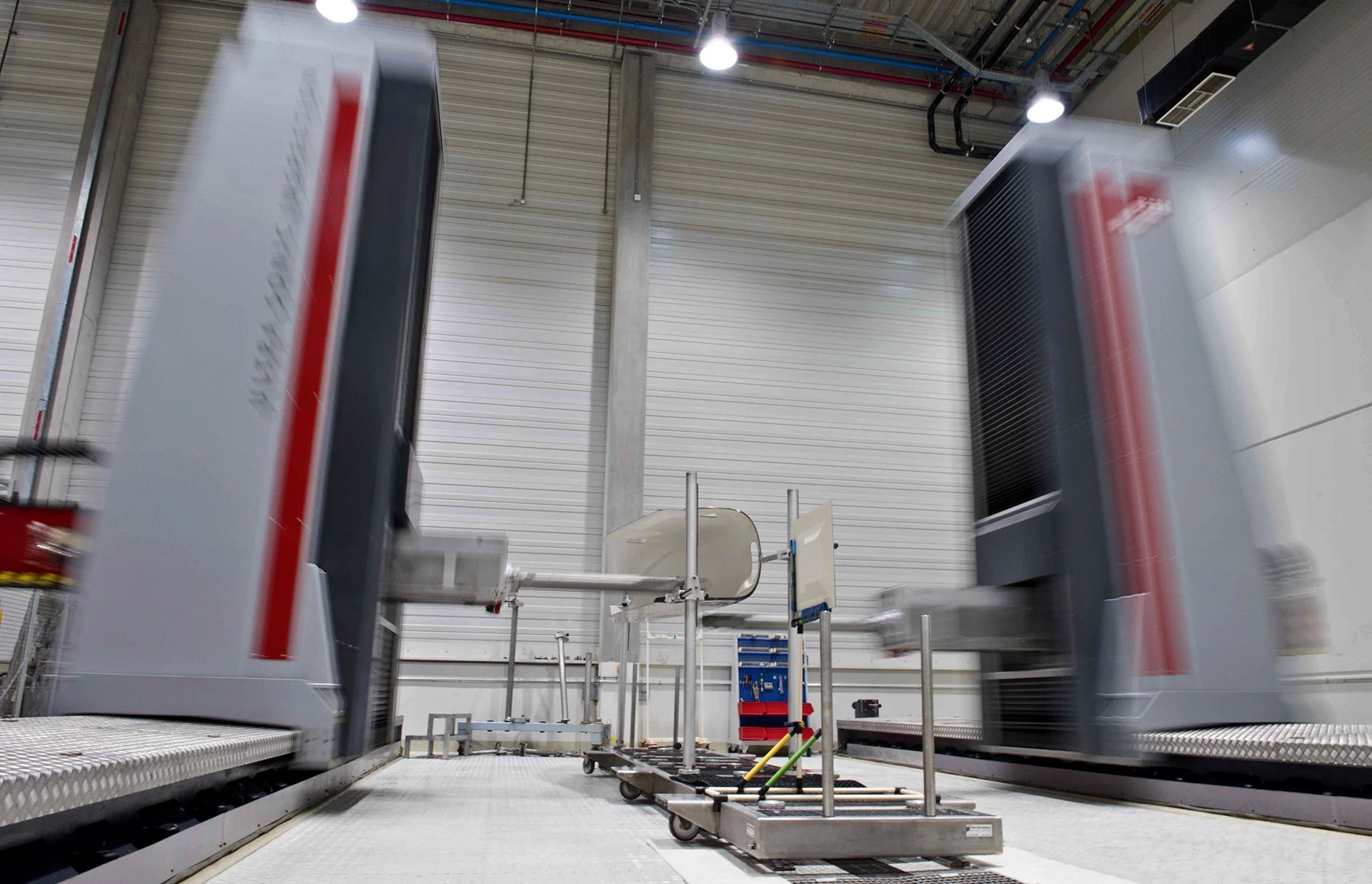
Paint Shop
- It would be easy to assume that the paint applied to aircraft parts is little more than a statement of our clients’ brand. However, paint plays an important role in protecting components from the elements, not least in the hugely variable environments and conditions which aircraft operate.
- At Strata, we’ve built a state-of-the-art paint facility, where the application of prime, anti-static/lightning strike protection, and high finish final coats can be applied with our signature accuracy and attention to detail.
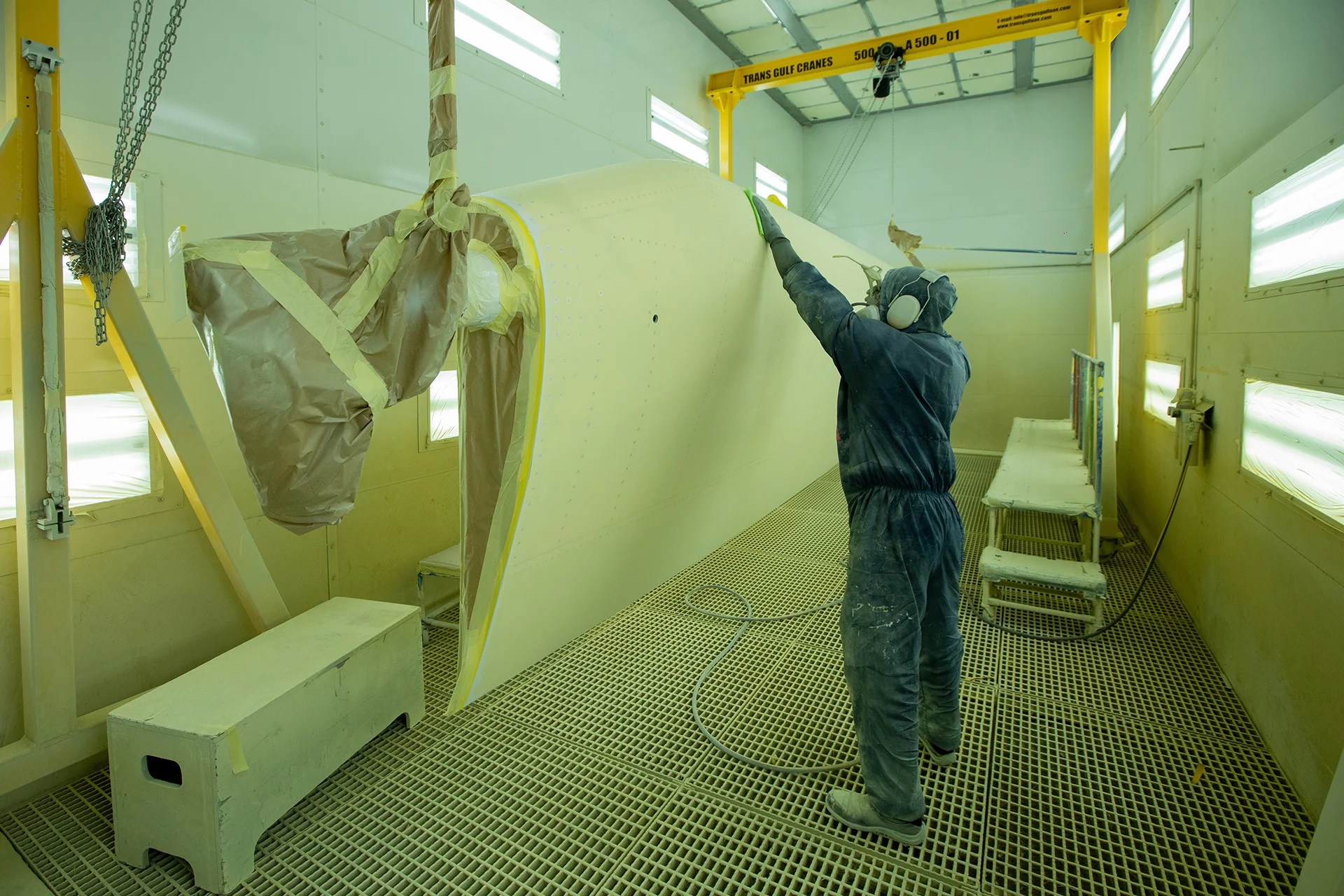
Assembly
- Our Assembly Area is where every aircraft component undergoes its final fittings of metallic parts, seals, and any other sub-assembly procedures.
- Our skilled technicians in the assembly area are responsible for the drilling, assembling and all interchangeability checks for each and every product, ensuring that the parts will fit onto the aircraft exactly as intended.
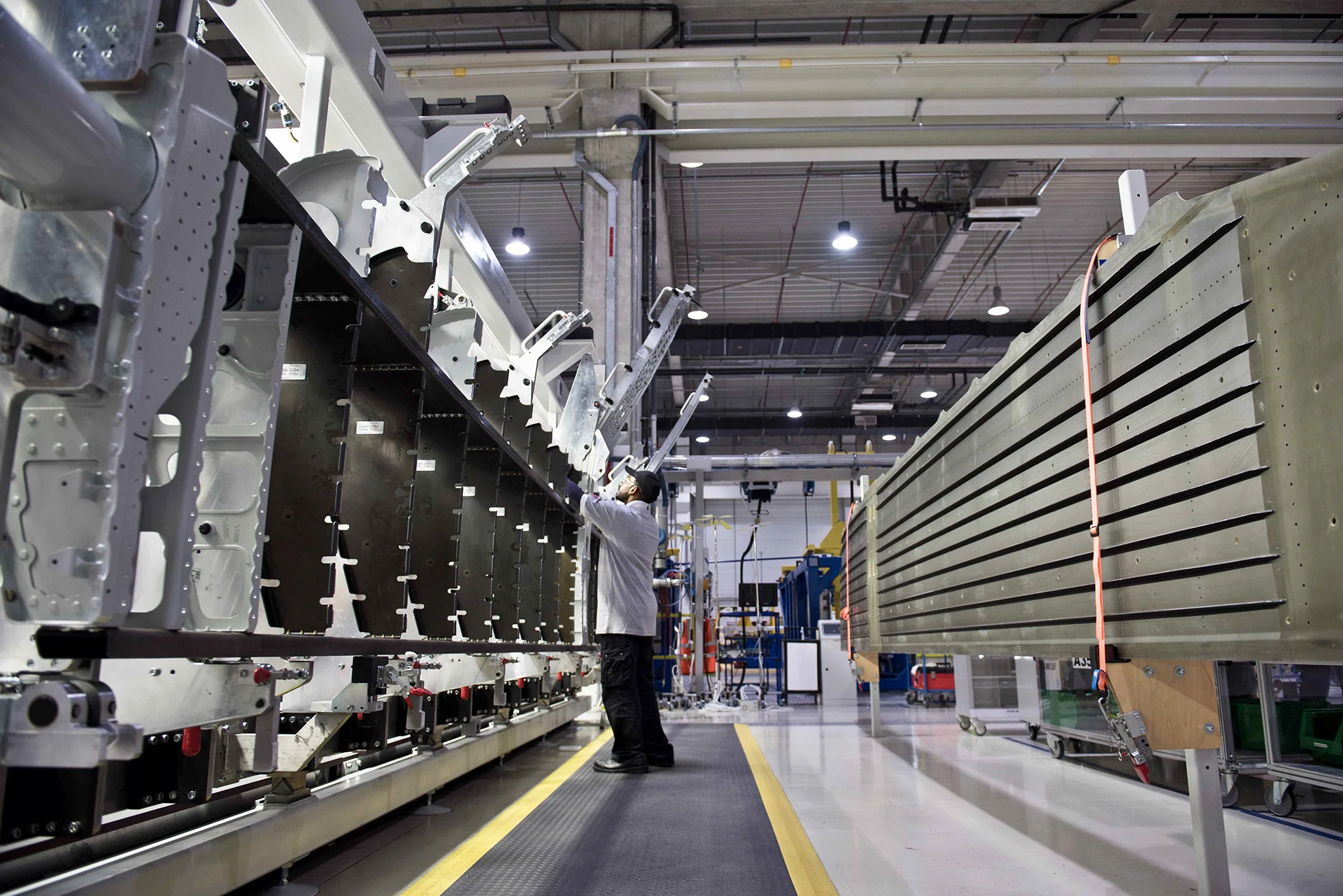
Research & Development
- The R&D unit at Strata powers our innovation, focusing on developing advanced manufacturing technology to build pathways to future programs.
- Launched in 2015, our R&D unit has forged meaningful collaborations with UAE universities, technology partners and valued OEM customers.
- With two state-of-the-art research labs – one at Strata in Al Ain and one in Khalifa University – our forward-thinking program covers additive manufacturing, advanced inspection techniques, optimized processing and machining of composite parts, robotic assembly, AI, data analysis and much more.
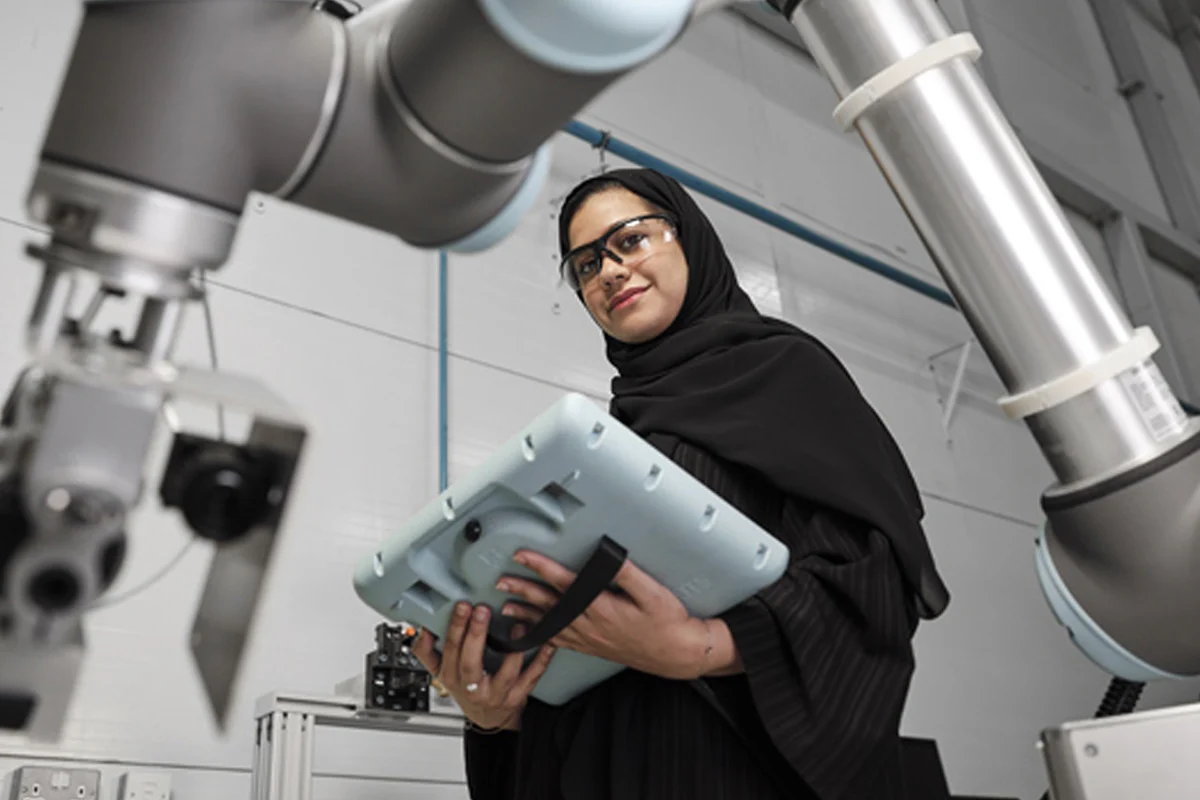